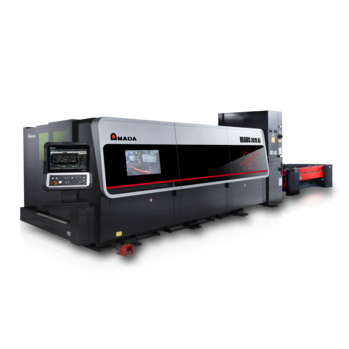
The market for sheet metal cutting machines has been experiencing some very interesting trends for years. In addition to strong themes such as automation, interconnection and remote monitoring, linked to the transformation of the industrial paradigm, the increase in the power of lasers has always been an element that directs the research of machine manufacturers. The reason is easy to understand: the market is demanding more and more power to increase cutting and breaking speeds, thus reducing the cost of the single piece. In addition, a greater power of the laser beam allows to manage different materials and, above all, the medium and high thicknesses, satisfying at best any need is manifested by the market.
AMADA has always met the needs of its customers, and this is why it has recently introduced on the market a model of ENSIS-AJ with 12kw laser power (3 4kw modules), alongside the 3, 6 and 9kw models.
The increase in power is aimed at maximising productivity, that is, cutting speed depending on the type and thickness of the material.
This does not mean, it is right to say, that 12kw is the solution to all needs, since the cutting phase is integrated in a much wider production process that includes different phases such as bending, painting and assembly. Only the observation and the "systemic" study of the process allow to identify the right solution according to your needs, a solution that is not necessarily the most powerful.
Given the bond with productivity, it is normal for the market to offer increasingly powerful machines over time. But the even more important aspect, on which to focus the attention, is the cutting quality that a 12kw model is able to guarantee on different materials and thicknesses. Considering the specific needs, we can therefore say that the right machine is the one that correctly balances speed, versatility and cutting quality. The greater power, in fact, must be managed in the right way to provide brilliant results, and AMADA responds to this need with a set of technologies that work in synergy to achieve all the goals mentioned and also one more: efficiency.
AMADA technologies that improve laser cutting
A key element of the entire ENSIS-AJ series, and therefore also of the 12kw model, is the VARIO technology, that is the variable laser beam control. The strongly innovative aspect is the ability to automatically adapt the “mode”, that is the density of the beam to the type and the thickness of the piece to be cut. All this, with a single lens and in an incremental way, in order to guarantee a tailor-made adaptation to specific cutting needs (material, thickness).
The beam then enters the fibre optic and passes through a system of auto-collimation (ACL) that defines with extreme precision the size of the spot and the position of the focus, generating a very precise cut and removing the molten material, resulting in increased quality of the cut edge.
Always in order to perfect the balance between power and quality, AMADA has created some proprietary technologies such as Silky Cut, which allows you to cut medium- high thickness stainless steel with a very high quality and without that roughness on the profile that is typical of fibre laser cutting.
Last but not least, do not forget the innovation of CFC technology, acronym of Clean Fast Cut. The goal for which it was developed is precisely the combination of quantity (speed), quality and also savings: CFC is based on a new cutting nozzle design that optimizes the assist gas flow, significantly reducing consumption. One problem with cutting thick is gas consumption, which obviously increases the cost of the workpiece.
Thanks to innovation, AMADA is able to accelerate cutting speed and also reduce consumption: thanks to CFC, ENSIS-AJ 12kw is able to cut iron in nitrogen with a reduction in gas consumption up to 70% compared to the conventional process.
With all these innovations, AMADA proves to support market trends but never to lose its innovative approach and vision on the entire production process, from which optimization derive the real benefits in terms of productivity, efficiency and profitability.