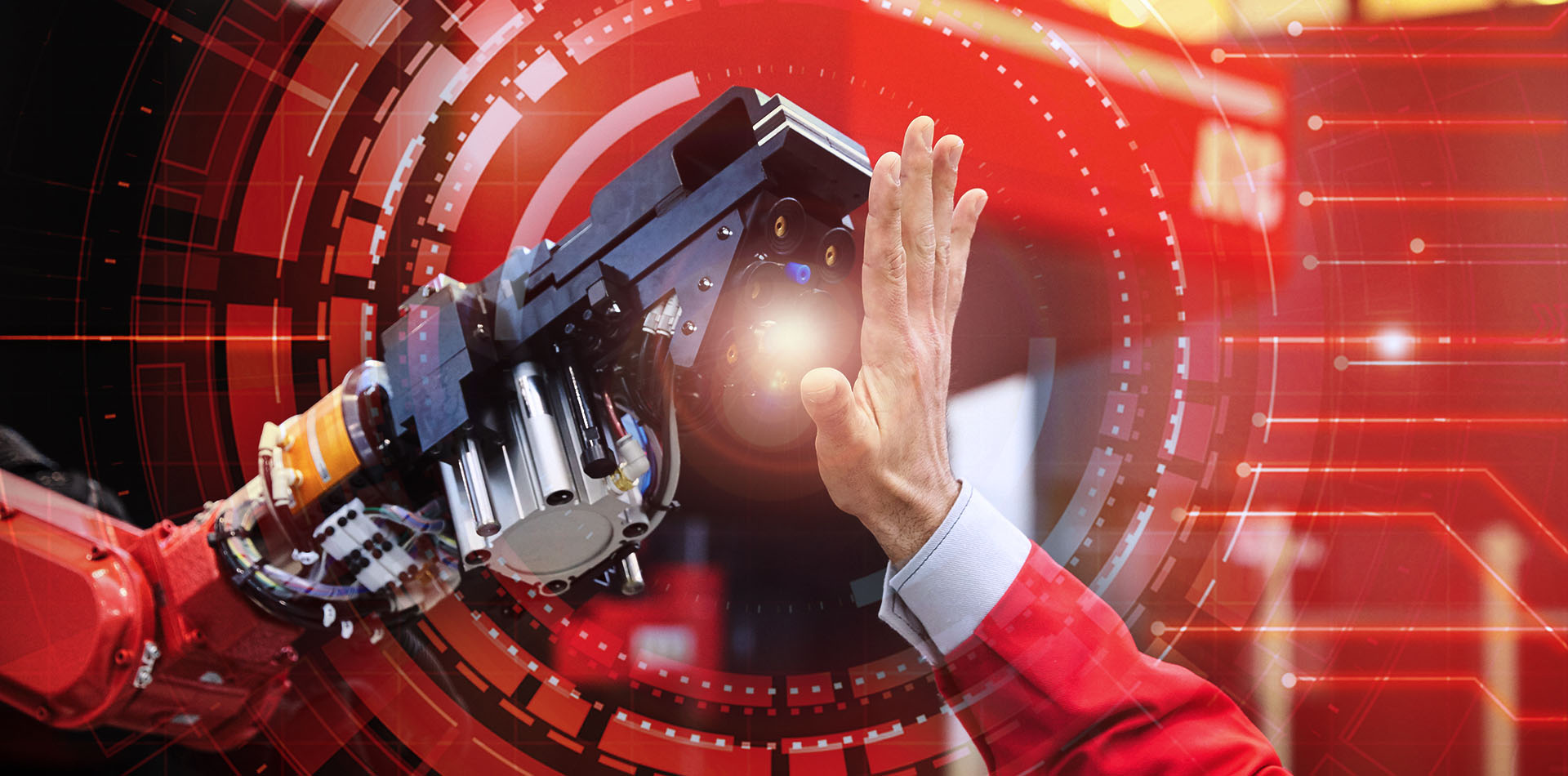
Our Industry 4.0 solutions to optimise your production.
The industry 4.0 paradigm, or smart manufacturing, continues to be a very successful trend and will be so in 2022. The most recent data, provided by the Observatory Transition Industry 4.0 of the Polytechnic of Milan speak clearly: if in 2020 the Italian market of Industry 4.0 has marked an increase of value of 8% driven by strong investments in IT technologies, 2021 aims for even better performance. Although reliable data is not yet available, the same source estimates (2021) a further acceleration of expenditure, between +12% and +15% compared to the previous year. Once again, IT technologies on the rise, with absolute dominance of Cloud Manufacturing (+25-30%), Advanced Automation (+15-20%) and Advanced HMI (+12-18%), while Industrial IoT, a true stronghold of Industry 4.0, begins to give ground because of its already pervasive spread.
The real protagonist of 2021 is Smart Working
Moving away - but only temporarily - from the shopfloor, 2021 was the year of the definitive consecration of the smart work model. After the emergency phase of the previous year, which had seen the 570 thousand Smart Workers of 2019 become 6 million in a few weeks, Smart Working is shaping new hybrid dynamics of work, based on the mixture of physical (office) and virtual experiences (collaboration platforms, connected tools, video-calls, etc.). As per script, smart work finds some resistance in cultural and organizational structures not ready to welcome it, but represents in any case the present and the future of work, also for the opportunities for efficiency and saving that opens to companies.
One of the trends of the moment, which we will experience in 2022, is the Industrial Smart Working, a theme connected to that of smart manufacturing. Industrial Smart Working wants to bring, into the world of operations and the factory, the paradigm of smart work, supported by a correct technological qualification and an adequate culture. We usually associate the theme of Smart Working to Office Automation, especially since in the first lockdown periods it was precisely the production lines and logistics plants that had the greatest tensions from the point of view of business continuity. But the situation is changing.
Smart Working applied to the shopfloor: science fiction or reality?
The pandemic has shown how disruption is real and companies need to invest in resilience. In the context of the Smart Factory, the application of the smart paradigm could generate benefits similar to those of the office work model, with a real reduction of safety risks.
If the theory is completely in favour of Industrial Smart Working, it is necessary to understand how much and if this way is practicable. To tell the truth, many smart manufacturing platforms, such as V-factory by AMADA, are moving in this direction, with a gradual but very effective path. This means that, experiments and specific cases aside, the hypothesis of completely managing a Smart Factory remotely is still impractical, but many supervision activities are, and it is in this direction that we are moving.
It was said at the beginning that a sector of Industry 4.0 on which many investments are focusing is those of Advanced HMI, or the innovative human-machine interfaces: augmented reality, for example, allows operators and line managers to acquire information about machine activities and their operating parameters by filming them with a smartphone or adopting a virtual viewer. In addition, by doing so it is possible to remotely control the quality (always with virtual viewer), or still establish a direct connection between the remote supervisor and the operator in the field, so that one can give instructions to the other and guide him in complex activities without the need to be present in the factory
V-factory and the remote control of the production process
We started from rather specific use cases, but more generally the whole Industry 4.0 paradigm is based on data and connectivity, then on the remote access and control of production systems. Thanks to AMADA’s V-factory, today it is not only possible to keep under control the operating conditions of a machine, evaluating key indicators for its performance, but also the entire production cycle using simply a smartphone, a tablet or a PC. The system, in fact, keeps track of everything: activities carried out, times, parts made, consumption, setup times, tools used and much more, using this data for real-time monitoring and also for predictive productivity analysis, such as to identify bottlenecks and inefficiencies to be resolved as soon as possible.
The cloud, for its part, is used not only because of its natural scalability, which is fundamental to process huge volumes of data and facilitate decision-making processes, but precisely to allow easy accessibility from outside combined with a unique solidity and levels of security online, if not better, than those of private infrastructure. Let’s not forget that among the smart manufacturing trends of 2022 there is undoubtedly cyber security, a direct consequence of the increasing convergence between the IT and OT worlds.
The end result is the possibility to remotely supervise the entire production process, as well as to intervene directly on individual segments and enable typical cases of Industry 4.0 such as predictive maintenance of machinery, which is offered as a service managed by AMADA technicians, who combine the specialized skills with the ability to monitor the machines in the factories of customers 24 hours a day. In this way, AMADA can intervene - strictly in smart form - with maintenance activities only when necessary and before the actual fault occurs.