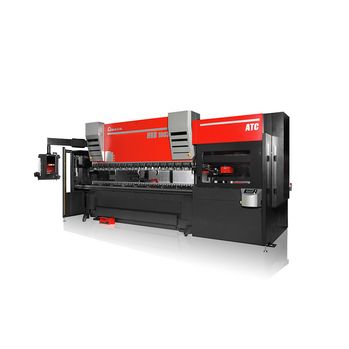
Sheet metal bending is a key step in the production process. It has always been, it still is.
Over time, however, the needs of the market have changed completely, from which new challenges that manufacturers must overcome to maintain levels of efficiency in line with business objectives.
In the past, the setup of the presses could remain unchanged for days, sometimes weeks. Today, producers have to juggle in a market characterized by extreme variability, smaller and smaller batches and almost constant urgencies that clash with their limits of flexibility and adaptability. Quality requirements are constantly increasing and there is an increasing pressure on delivery times, with the result that a machine can perform various different processes per single shift. In this state of affairs, inefficiencies are the order of the day: errors, excessive downtime, qualitative problems can undermine profitability, but also the reputation of the company. In the era of production 4.0 there is no room for inefficiencies: it is no longer a question of differentiation, but of the ability to withstand in an extremely competitive context.
Sheet metal bending, energy efficiency and the role of automation
So how do we approach the current challenges of sheet metal bending? First of all, it will seem obvious, but we need machines that guarantee high performance, speed and quality with low power consumption, that is, with high standards of energy efficiency. In this respect, a specific mention goes to the HRB-ATC series, equipped with hydraulic drive and inverter motor able to ensure an extreme efficiency of bending operations with a simultaneous reduction in energy consumption of at least 20% compared to traditional models.
A separate, but equally important, chapter is dedicated to automation, which is made possible by the strong technical evolutions that have affected the sector. Automation is the antithesis of inefficiency, it is the possibility of delegating to the machine the activities with little added value allowing operators to exploit their skills for more complex and professionally satisfying operations. If well designed and implemented, automation is a benefit for everyone.
Tool setup, the ideal candidate for automation
It is now clear to professionals that the first area in which to intervene is the passive part of the production cycle, starting from the equipment (or setup) of the machines.
In sheet metal bending, the setup is traditionally performed on a stationary machine and is a critical operation still carried out manually, with unpredictable times and all that follows in terms of operator productivity, cost of finished product and process efficiency. When downtime is not predictable, it becomes difficult to calculate the cost of the products, on which the company’s commercial strategies depend. Tool setup is therefore an ideal phase for automation, and it is not by chance that the HRB-ATC series of AMADA hydraulic press brakes has one of the main competitive advantage factors in the automatic tool change (ATC).
The system reduces downtime by automatically setting up the tools, that is, transporting punches and dies from the tool warehouse to the machine and vice versa using two pairs of robots and relying on instructions given by software. In addition to the obvious impact on safety and production efficiency, which is especially evident when different equipment is required per shift, two other factors (at least) must be taken into account:
Sheet metal bending and the role of offline programming
In the world of sheet metal bending, another important aspect that affects production times and efficiency is the programming of the machine, a complex activity that is usually carried out with machine stopped.
The HRB-ATC series of AMADA bending machines is based on the VPSS 3i Bend software, which in addition to functional completeness and the use of automation, allows to program the press in totally offline mode, that is, from the technical office and during the time of operation of the machine itself. This brings important benefits not only in terms of non-stop productivity, resulting in shorter lead times and reduced cycle costs, but also in terms of engagement and the creation of new operating modes
working in offline mode allows more experienced operators to program several machines at the same time and then to make the most of their time and skills acquired over the years; for their part, employees with less experience will instead be guided by the machine and its multi-touch numerical control in the correct execution of operations, resulting in the reduction of errors and - above all - gradual and progressive enrichment of skills.