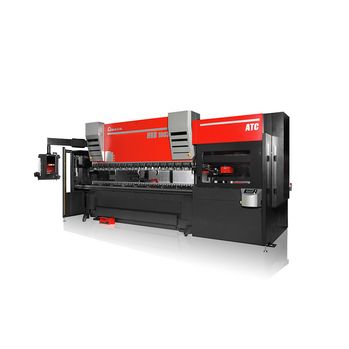
According to a study by Deloitte and The Manufacturing*, by 2030 there will be 2.1 million vacant positions in American industrial production, for a total cost of $ 1 trillion resulting from the inability to meet demand. Curiously, the producers say that finding the right professionalism is increasingly difficult (36% more than in the pre-pandemic era) and that it is also to retain the best talents. All this feeds the phenomenon of the Skill Gap, that is the misalignment between the competences demanded from the demand and those offered from the market. Misalignment that, as anticipated, can be very expensive for the entire compartment.
The Skill Gap in sheet metal bending
The Skill Gap is particularly felt in the world of sheet metal bending, where finding qualified employees and retaining them in the company has always been difficult. Among the reasons, the complexity of programming the machines, as well as all the specific skills related to the executive aspects of their role. The planning of a press brake has in fact always required important technical skills, of which the market was and is miserly. Often, such skills are acquired with years of experience, which makes the experienced bender a very rare figure and an invaluable asset for many companies.
The solution: enhancing skills and experience
How best to deal with a problem that will not solve itself over time? The most intuitive, but still valid, answer is the strong investment in internal training. The benefit of a continuous learning path is the autonomy of the employees, who may be able to plan and produce according to projects and contingent needs.
The second possibility, which does not exclude but strengthens the previous one, is the maximum enhancement of skills and experience, a logical principle but not always put into practice. The most interesting hypothesis, which also has a strong impact on production efficiency, is to program the machines offline, but above all to allow experienced benders to program more than one at a time and to distribute the various programs on different machines depending on the needs and orders.
This type of approach offers various benefits: the experience of the operator is valued to the maximum, the quality of the workmanship is maintained very high and the less experienced operators are guided in the executive phase, in turn acquiring useful skills for subsequent work. In addition, the company suffers less the Skill Gap, can make the most of its operators and gradually accompany the new grafts towards their professional evolution.
In order for this approach to be translated into practical terms, it must be fully supported by the bending process management software. This is the case of HRB-ATC and the VPSS 3i Bend software (Virtual Prototype Simulation System), which allows the offline programming of bending and interfaces with other AMADA solutions to optimize the entire production flow. In the case of HBR-ATC, this is further simplified and made more efficient by the use of the latest multi-touch CN with an 18.5-inch diagonal display.
Automation to retain the best resources
Returning to the research of Deloitte, it emphasizes that the difficulties of the companies do not concern only the acquisition of talents, but also their permanence in the company. Here, too, there are many considerations that affect retention: wages, the working environment, shifts, jobs and, more generally, the company’s ability to create a healthy, safe and engaging work experience.
The phenomenon must be tackled at several levels, but the creation of a safe and comfortable environment undoubtedly affects the activity of equipping the machines, which is not only expensive for the company, but notoriously tiring for the bender, especially in the era of micro-batches. A machine like HBR-ATC can help companies in many ways: maximizing production efficiency, making predictable times and costs, and also retaining their best talents. In fact, they no longer have to deal with repetitive, tiring and less value-added activities, instead being able to concentrate on developing their skills and, consequently, on their career.
* source: Deloitte