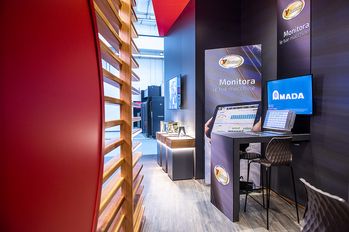
Non c’è dubbio che l’espressione Industria 4.0 sia ormai entrata nel lessico comune. Al tempo stesso, è piuttosto complicato far convergere in una ‘definizione da manuale’ un cambio di paradigma così importante e pervasivo; c’è chi pone l’accento sulla robotica, chi su inediti livelli di automazione e chi preferisce soffermarsi sulle tecnologie di ultima generazione pensate per popolare una smart factory.
La verità è che l’espressione Industria 4.0 identifica un modello industriale abilitato dalle tecnologie di ultima generazione e rivolto alla massimizzazione dell’efficienza, della produttività, della qualità e al miglioramento delle condizioni di lavoro. Di fatto, essa rappresenta il punto più alto della digital transformation applicata all’ecosistema produttivo: per questo motivo, Industria 4.0 non è né robotica né Intelligenza Artificiale, ma un nuovo paradigma industriale abilitato da queste e molte altre tecnologie di frontiera. È inoltre un fenomeno di grande successo: si stima che il mercato delle soluzioni di smart manufacturing possa raggiungere i 384 miliardi di dollari nel 2025, ma soprattutto che possa crescere con un CAGR del 12,4% dal 2020 al 2025 (fonte: markets and markets), a testimonianza di quanto l’industria si stia affidando a soluzioni tecnologiche avanzate per massimizzare la propria efficienza, ridurre i lead time, accelerare il time-to-market e, cosa tutt’altro che secondaria, mantenere elevata – o addirittura migliorare – la qualità del prodotto.
Industria 4.0 e l’universo data-driven: benefici e soluzioni
Rispetto al paradigma di Industria 4.0, le tecnologie avanzate rappresentano dunque il fattore abilitante. A livello tecnico, un aspetto peculiare di una smart factory è il progressivo e costante avvicinamento tra i segmenti (tradizionalmente separati) dell’Information Technology (IT) e dell’Operational Technology (OT), laddove quest’ultimo racchiude tutte le tecnologie dedicate alla gestione, al controllo e all’automazione degli impianti industriali.
Tutto ciò significa, all’atto pratico, che oggi fondamenti di Industria 4.0 (o di smart manufaturing che dir si voglia) sono ‘anche’ tecnologie tipicamente appartenenti all’universo IT e della data science: l’Industrial Internet of Things (IIoT), con i suoi attuatori e sensori in grado di rilevare in tempo reale le condizioni di esercizio delle macchine, le reti industriali – in quest’ambito c’è molta attesa per il 5G -, le piattaforme cloud di analisi dei dati intrise di Machine Learning, i sistemi di Computer Vision per il controllo qualità, i famosi digital twin, la realtà aumentata e l’edge computing, che è fondamentale per le attività che richiedono una latenza pari a zero, o quasi.
L’elenco delle tecnologie che abilitano o si troverebbero a proprio agio in un modello smart o 4.0 potrebbe andare avanti a lungo, ma qui ci interessa evidenziare un aspetto che le accomuna tutte: la centralità del dato. Il processo di acquisizione, trasferimento ed elaborazione/analisi del dato è il fondamento del modello industriale 4.0, che di conseguenza è a tutti gli effetti un paradigma data-driven. I sensori dei macchinari (IIoT), per esempio, si occupano della raccolta in tempo reale delle informazioni e, tramite gateway e reti industriali, li trasmettono in cloud (o edge) per l’elaborazione, che a sua volta si può avvalere di Data Lake e algoritmi di Intelligenza Artificiale: per chi dirige la produzione, per il business ma anche per gli addetti alle linee, il risultato pratico è un quadro costantemente aggiornato sul ciclo produttivo, sulla “salute” delle macchine, sui coefficienti di produttività e sull’impegno di tutte le risorse, che siano macchinari, materie prime o addetti in carne ed ossa. Ecco dunque i primi indubbi benefici del modello 4.0: visibilità, controllo, prevenzione, massimizzazione delle performance, delle risorse, dei consumi e dell’efficienza, cose possibili solo se esistono dati su cui operare e se questi vengono elaborati e valorizzati nel migliore dei modi.
Industria 4.0 e soluzioni AMADA, un binomio perfetto
Le soluzioni AMADA sposano perfettamente il paradigma di Industria 4.0, sfruttando il dato per massimizzare le performance del ciclo produttivo, fornire visibilità sulla produzione interconnessa e ottimizzare il controllo sulle macchine, anche a livello preventivo.
Il sistema V-factory, composto da un Connecting Box e dal portale My V-factory (accessibile da PC e dispositivi mobile), acquisisce e condivide tutti i dati essenziali per un controllo preciso e puntuale della produzione: stato attuale e disponibilità delle macchine, carichi di lavoro, storico della produzione, eventuali segnali che consigliano un intervento di manutenzione e un’analisi integrata del processo produttivo, comprensiva di valutazioni sul consumo dei materiali e su quelli elettrici, così da prendere le migliori decisioni basate sui dati.
V-factory fornisce dunque visibilità sul processo produttivo e permette il monitoraggio remoto degli impianti con una semplice connessione Internet: tutto ciò assume importanza centrale in ogni circostanza, ma soprattutto nei cicli notturni e in quelli senza operatore. L’analisi dei dati, che V-factory fornisce in tempo reale, è essenziale per soddisfare le esigenze di svariate funzioni: di un direttore di produzione, intento a massimizzare produttività ed efficienza dell’impianto; di un imprenditore, la cui attenzione va soprattutto all’eliminazione delle inefficienze, abbassamento dei costi e rispetto delle tempistiche produttive; ma anche degli operatori, che possono ottenere i migliori risultati possibili limitando al minimo gli imprevisti.