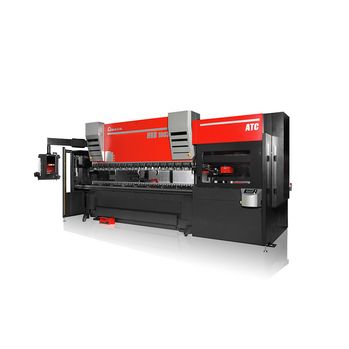
In 2022, sheet metal processing companies are facing several challenges that affect their strategies and day-to-day operations. First of all, the scenario is very competitive, and a continuously decreasing margin is added to an ever higher demand for quality. In addition, the market demands great reactivity, the ability to manage real micro-lots and a very high level of customization.
All these factors and many others (e.g., increased raw material costs) push businesses towards maximizing efficiency. Starting from the individual stages of processing, the goal must be to optimize the entire process, focusing on high-performance, reliable and technologically advanced machines: that is, to make available to productivity all the progress that has led to paradigms 4.0.
AMADA HRB-ATC, the innovation in the bending world
In terms of innovation and productivity, the HRB-ATC series of AMADA bending machines are a benchmark. While the cutting phase (blanking) is usually very efficient, many potential problems are concentrated in bending, so that it is considered the most complex macro-machining of the process. In addition, bending is full of micro-processes that have a very strong impact on productivity: think of the research and tooling of the tools, the machine setup and all the necessary configurations to start the operation. This not only wastes time, but also interrupts automated processes, introducing the possibility of errors and inefficiencies.
AMADA HRB-ATC is the solution to all these challenges. First of all, the bending machine is integrated into the AMADA universe and into its manufacturing virtualization paradigm that extends throughout the entire process and not just in a single step. The concept of the machine (and the ecosystem) is inspired by the concept of intelligent production thanks to the connection and synergy with other machines, the use of the VPSS 3i system, the integrated cameras and the numerical control with a large 19' multi-touch display (used to control the machine and share instructions to operators), HRB-ATC allows the company to manage the challenging market conditions in an agile and effective way.
HRB-ATC and the automation of micro-phases
The AMADA HRB-ATC range embraces the concept of micro-phases automation, in which - as we have seen - a large part of inefficiencies lurks. HRB-ATC can be programmed remotely, so as to guide the operator towards the best possible execution; moreover, it has its own Automatic Tool Changer to independently carry out the set-up operations according to the machining to be carried out. The result is a reduction in time and costs, a longer tool life, a reduction in errors and fatigue. In one word only: efficiency.
The HRB-ATC series machines (HRB-1003 ATC and HRB-2204 ATC) are also equipped with the latest generation of technical and safety features. For example, magnetic release heads are able to combine maximum performance with operator safety. The models in the HRB-ATC range also pay great attention to the issues of reducing waste and sustainability: compared to traditional bending machines, the hydraulic drive system with inverter guarantees energy savings of up to 20% and, since the hydraulic circuit is driven on demand by the bending cycle, this improves the management of hydraulic components, resulting in saving for the company and a positive impact on the whole environment.