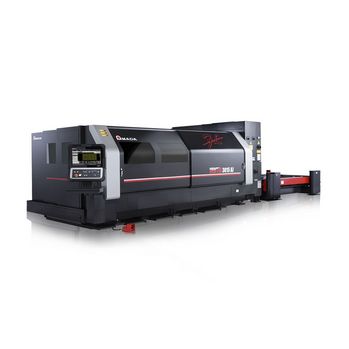
In the era of Industry 4.0, data analysis is - or should be - the main decision support tool. Although the focus is mainly on the interconnection of machinery, automation, remote management, IoT and other innovative cases, the paradigm 4.0 is in fact a continuous path of generation and enhancement of large volumes of heterogeneous data..
Data Analytics and its value as decision support
In the context of operations, companies make hundreds of decisions every day. Some concern planning and strategy, others - the most numerous - are operational: scheduling of the work plan, organization of available resources (including human), sequence planning, handling and storage of raw materials, semi-finished and finished products.
In the era of digitalization of any process, you might think that all business decisions are data-driven, that is, data-supported. However, it is only a small part, that which affects the strategic area: all the others are still based on experience, competence and instinct, but certainly not on data. This is what data analytics is all about: transforming data volumes into information, building knowledge and making decisions in everyday operations.
But what is limiting companies from realizing the full value of data? It may seem strange in 2022, but the first limitation is the scarce diffusion of the data culture, which is often present only at the directional level and feeds the mentioned phenomenon. Then, of course, there are technical challenges to face, related to data acquisition, data governance, end-to-end security, the quality of data and the ability to process them in real (or almost) time, extracting and spreading knowledge horizontally.
Sometimes, the limit depends on the silos at the machine, line or company division level, or even just on the fact that the analysis systems are separated from the executive tools used every day. Each of them has, as a rule, its own intelligence, but decisions presuppose the integration of data from different machines, or sources that you say you want.
Data analysis to optimize processes
Optimizing production from a data-driven perspective is the ultimate goal of manufacturing. Not only for a matter of efficiency, that is to optimize the delicate balance between productivity and costs, but above all to satisfy the needs of flexibility and agility required by the market: a priority order to be included in the work plan, manage microbatches in the best way, adapt quickly to the breakdown of a machine and so on. Data analytics are a source of resilience.
Not only that: the analysis of data from the universe of machines is what enables some characteristic cases of the world 4.0 such as predictive maintenance, to which we have dedicated an ad hoc deepening, as well as virtualization models of the production process and contextual implementation of the so-called digital twins, which allow to simulate real operating conditions and new production models by evaluating (in data-driven mode) their outcomes before going into production and - potentially - before wasting time and raw material.
Field data are the basis of any virtuous path in the world of operations: from the improvement of the efficiency of the machines to the management of resources, up to all the optimizations in the field of internal logistics, where the positioning of the finished product (storage) and picking according to precise logics (FIFO, FEFO...) can have an extraordinary impact on lead time and therefore, in very practical terms, on the moment when the final customer receives the processed product.
AMADA solutions for data-driven production
AMADA has long decided to lead the progressive transformation of companies towards the 4.0 models, in the certainty that the end-to-end digitalization of the production process had a major impact on the productivity and profitability of its customers.
The concept that inspires us is transparency: thanks to the continuous acquisition and valorization of data, the V-factory platform is not only a tool for visibility, but also for data-based decision support driven easilydistributable to all those involved in the process. If a time the remote connection meant to know only the operating status of the machinery, V-factory allows a thorough 24 hours monitoring of the entire production line, so as to precisely define schedules, purchase orders for raw materials, preparation of warehouses, resource shifts and also the best paths to accelerate the productive lead time.
The acquisition of data and its transformation into insight also enable the innovative cases mentioned above, namely the prevention of failures and the related predictive maintenance. Considering the costs of downtime, being able to anticipate any problems and plan correctly the solution has an extraordinary value not only from an economic point of view but also from a reputational point of view: the company that respects the times of delivery, despite unavoidable unforeseen that are part of the operativity, is placed on the market with a force that the competitors do not have.
Last but not least, data analysis also means enabling efficient remote support and creating a partnership with the manufacturer of the machines, which having available (in real time) the operating data is not only able to prevent failures, to send support on field and to order any spare parts before the failure occurs (think about all the time saved), but also to monitor the entire process and provide useful suggestions (data-driven) aimed at its optimization, contributing to the success of their customer.