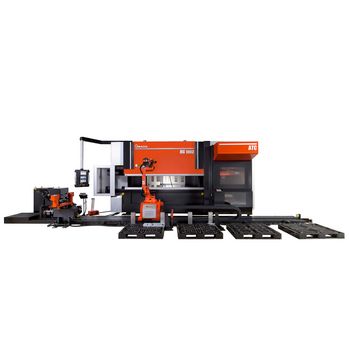
Why is the issue of automatic setup important?
Let’s start by saying that today the market is increasingly competitive and dynamic, and this inevitably creates pressure on production activities, which today is required agility and efficiency that until yesterday were unthinkable. True success is measured by the ability of operations to meet - and sometimes anticipate - the needs of an unpredictable market that makes planning extremely complex: ever smaller batches, urgent orders to be met, lead time to shorten of continuous and, obviously, a constant pressure for the discouragement of the wastes and the rejects, that is for the cost reduction.
Optimizing production in terms of time, quality, costs and - of course - compliance with deliveries means perfectly governing a complex ecosystem, made of machinery, information systems, suppliers and operators, each of which has a percentage of responsibility towards the final result. But if we want to limit the discourse to machines, and therefore to grasp a specific aspect of this perfecting activity, we should definitely talk about automatic setup, with a particular attention to bending machines.
Automatic setup, a concrete(and possible) goal
The setup of the machines, although inevitable in the context of manufacturing, translates into a cost that is far from marginal for the company, and it is not by chance that we have always sought useful strategies for its optimization. Any number? Speaking of bending machines, we can safely assume that on 10 hours/machine, just over 3 are actually dedicated to bending, with everything else employed to find the tools, choose them, assemble them, that is, in fact to equip the machine. Now, stopping the production is, in itself, an important cost that is reflected on the price of the product and, therefore, on the competitiveness of the company, but we must also expect that in the installation you can damage the tools, errors occur due to manual procedures and fatigue that after a while inevitably occurs. This too has a cost, and certainly not negligible.
Historically, companies have taken two paths in order to reduce setup costs: one relating to the optimization of the setup itself, the other of production planning. The first category includes, for example, the famous SMED (Single Minute Exchange of Die) methodology born in Japan shortly after the middle of the last century and which is based - simplifying - on a subdivision of the activities between those that can be performed by machine in operation and those that require a stop: correctly divide the activities into the two categories, performing them efficiently and reducing (with various precautions) those that require the machine downtime leads to a noticeable reduction in setup time, up to 50%. To the second category belongs instead the efficient government of the production through executive information systems: the Manufacturing Execution System (MES), that is the acronym of reference in this context, usually allows a precise planning/scheduling of the production phases, optimizing them in order to avoid the greatest number of machine stops due to the setup.
Automatic setup: AMADA solutions
The final solution is to apply automation to the setup of machines, which is true for bending machines, but also - for example - for punching machines and combined machines. In the first case, automatic setup means that the machine itself is prepared for the next machining by a very fast tool setup and without the operator having to do any manual operation. An eloquent example of this is the HG-ATC AMADA bending machine, equipped with the Automatic Tool Changer (ATC): the machine, in fact, carries out the quick setup of the tools according to the instructions obtained from the production sheet; To this, HG-HTC adds the automatic tool block with hydraulic clamps and the possible inverted mounting of the tools.
A machine like HG-ATC is perfect for batch processing of variable sizes and with a complex tool layout: in the latter case, in fact, a manual setup could add up to rather long times even potential setup errors, from which all the consequences of the case. HG-ATC, on the other hand, is able to complete the most complex setup in less than 2 minutes, ensuring maximum precision, reliability but also intelligence, since among the automatic setup features of the machine there is also the exploitation of tools possibly already mounted.
The benefits are obvious:
the automatic set-up leads to reduced times, shorter lead times and less costs to bear, but also to more efficiency and safety within the production lines, an aspect far from secondary. Finally, automation simplifies operations: although it is always advisable to entrust the management to specialized personnel, automation increases flexibility and agility within the shopfloor, For example, by making up for an unforeseen absence without interruption or drastic drop in productivity.
Watch the recording of our ATC webinar: a changing philosophy ... automatically!